What Is The Scrubber Fitting Process? Find Out With This Detailed Explanation
IMO regulations from January 1, 2020 require all ships to achieve an SO2 emission rate in equivalence of fuel that has a sulphur content of 0.5% from the current permitted 3.5%. In SECA areas, this level requires the use of fuel having 0.1% sulphur content
There were two options for ship owners, changing to a more expensive low sulphur fuel or installation of EGCS (exhaust gas cleaning systems) or gas scrubbers.
The work behind the scenes begins four to six months in advance of any actual scrubber installation.
A typical EGCS installation requires the main engine and the auxiliary engine exhausts gases to be scrubbed to meet the IMO requirements
The work behind the scenes begins four to six months in advance of any actual scrubber installation.
Relevant technical information is requested from the ship to determine the sizing of the prospective scrubber, followed by a 3D scan which is used for creating a feasibility study that is approved by the client.
Good practice is to visit the ship well in advance of her arrival to the installation yard
This includes the exact siting of the scrubber and the ancillary equipment associated with the system including sea water pumps, monitoring and control equipment and the piping layout
Next stage is the creation of a 3D model that clearly shows where all the items are to be installed on the ship. This is the most challenging part of the entire project because any clashes require last minute design alterations and modification of pipes that could result in delays.
From experience we here at Pacific Green Marine, have learnt that good practice is to visit the ship well in advance of her arrival to the installation yard to counteract this and iron out all the issues.

A computational fluid dynamics (CFD) analysis is carried out to determine the placement of the new overboard discharge openings in order to meet the IMO guidelines of achieving a pH value of 6.5, four metres away from the ship side in sailing conditions. This is a theoretical calculation carried out by approved companies
All new design drawings and associated documentation are sent for class approval.
The scrubber with its protective enclosure and the piping (glass reinforced epoxy piping
for the scrubber wash water drain lines is preferred due to the high acidic nature of the effluent) are then prefabricated well in advance, so the project can be delivered within the time agreed, usually ranging from 25 – 45 days, depending upon the size of the vessel, the complex nature of the project and the yard personnel availability.
Some owners have opted for the “naked scrubber” option
The latter has been a challenge for all installers because of the last-minute rush by ship owners and operators to meet the January 1, 2020 deadline of the IMO regulations
Some owners have opted for the “naked scrubber” option. This does not have any steel enclosure on deck. With this option, special instrumentation is required in the exposed areas to counteract weather conditions
The installation generally begins with a ‘kick-off’ meeting between all parties concerned.
These include the ship owner’s representatives, scrubber supplier’s project manager and design team and the shipyard’s commercial team and their project manager along with their technical teams. This is a very vital stage because all technical issues are discussed, work scope agreed, and a project plan created with specific timelines for each stage of the installation
Once the ship arrives in the yard, the technical teams board the vessel for a full survey to establish whether any clashes or issues could be encountered.
If there are any found, the design is modified and class approval is obtained for these changes. They usually involve the positioning of the overboard discharge openings.
Once the project commences, the typical day begins with a shipboard morning meeting that is attended by the yard’s commercial manager, the project manager, yard technical supervisors, the scrubber supplier’s project manager, ship owner’s representative and senior ship staff. Safety issues are discussed, followed by scope of work for the day and plans for completion of these tasks
Through each day, our project manager inspects various jobs being undertaken, ensuring that the installation is being carried out in accordance with Pacific Green’s design criteria
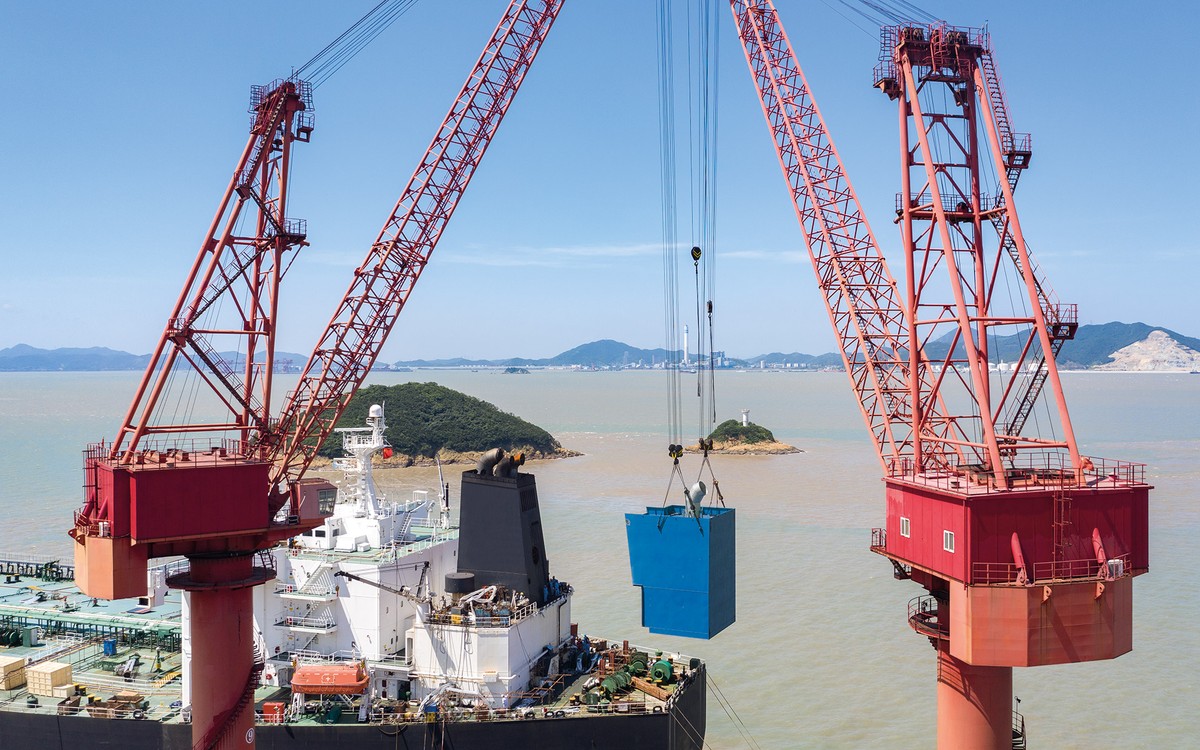
Work begins with the modification of the existing exhaust pipes. Bypass dampers are installed to allow the gas to flow through the scrubber while having the option to bypass the scrubber in the unlikely case of any failure. This keeps the ship fully operational in all conditions
The scrubber is fitted in place and connected to the exhaust piping. The existing ship funnel has to be modified to accommodate these changes. The protective enclosure is finally put in place and stitched to the existing funnel structure by welding.
A comprehensive harbour trial is carried out to determine the integrity of the new installation
Under deck, the new sea water pumps and all associated piping and valves are installed. The ship is moved to a dry dock for three to six days to cut new openings for the scrubber wash water overboard discharges. In most cases, a new opening for a sea water supply (a sea chest) to the scrubber has to be fitted and this is mounted at the same time.
Fitting of control cabinets for the new equipment along with electrical cabling is carried out in conjunction with all other works being carried out. Monitoring and measuring equipment are installed in the relevant sections of the pipes and the actual scrubber itself.
As each section of the system is completed, testing is carried out to save time on the final commissioning.
Once all the equipment has been installed and all systems commissioned, a comprehensive harbour trial is carried out to determine the integrity of the new installation.
The ship then leaves the yard for a sea trial. This usually includes a team from the scrubber supplier’s side, some shipyard workers for any mechanical fixes that may be required, the ship owner’s representative and a surveyor from the classification society.
The new system is put through its paces during the sea trials, test results being recorded at different engine loads and the system is signed off by the surveyor and the owner’s representatives. This time is also used to train the ship’s engineers in the operation of the new equipment
Effluent water samples are collected and sent to an independent laboratory for analysis
A final international air pollution prevention certificate is issued once the water test results are received.
And this brings the project to its final conclusion. Now it’s time to save money!
With thanks to Khushroo Bhandari
Would you like to discuss more?
Our global team of advisors with years of combined experience in the marine sector are on hand to discuss your project.